Технологијата за сечење на плочки, како клучен чекор во процесот на производство на полупроводници, е директно поврзана со перформансите на чипот, приносот и трошоците за производство.
#01 Позадина и значење на сечењето на вафли
1.1 Дефиниција на сечење на вафли
Сечењето на плочки (исто така познато како scribing) е суштински чекор во производството на полупроводници, насочено кон делење на обработените плочки на повеќе поединечни чипови. Овие чипови обично содржат целосна функционалност на колото и се основните компоненти што на крајот се користат во производството на електронски уреди. Како што дизајните на чиповите стануваат посложени, а димензиите продолжуваат да се намалуваат, барањата за прецизност и ефикасност за технологијата за сечење на плочки стануваат сè построги.
Во практичните операции, сечењето на вафли обично користи алатки со висока прецизност како што се дијамантски сечила за да се осигури дека секоја калап останува недопрена и целосно функционална. Клучните чекори вклучуваат подготовка пред сечење, прецизна контрола за време на процесот на сечење и проверка на квалитетот по сечењето.
Пред сечењето, плочката мора да биде обележана и позиционирана за да се обезбедат точни патеки на сечење. За време на сечењето, параметрите како што се притисокот на алатот и брзината мора строго да се контролираат за да се спречи оштетување на плочката. По сечењето, се спроведуваат сеопфатни инспекции за квалитет за да се осигури дека секој чип ги исполнува стандардите за перформанси.
Фундаменталните принципи на технологијата за сечење на плочки опфаќаат не само избор на опрема за сечење и поставување на параметрите на процесот, туку и влијанието на механичките својства и карактеристики на материјалите врз квалитетот на сечењето. На пример, плочките од диелектричен силикон со низок k, поради нивните инфериорни механички својства, се многу подложни на концентрација на стрес за време на сечењето, што доведува до дефекти како што се кршење и пукање. Ниската тврдост и кршливост на материјалите со низок k ги прави посклони кон структурни оштетувања под механичка сила или термички стрес, особено за време на сечењето. Контактот помеѓу алатот и површината на плочките, заедно со високите температури, може дополнително да ја влоши концентрацијата на стрес.
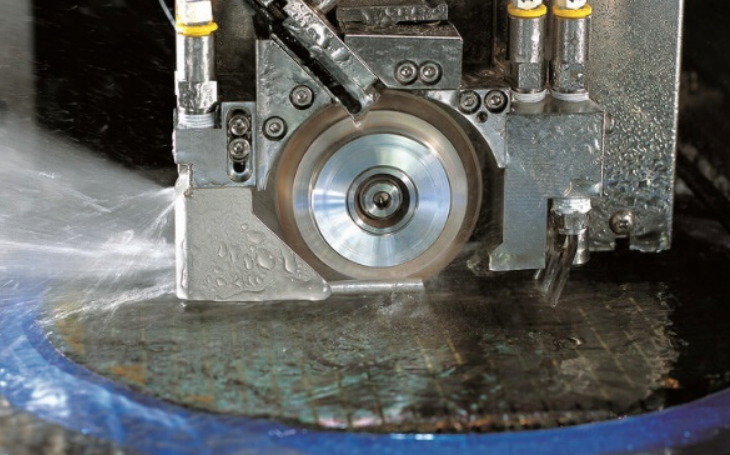
Со напредокот во науката за материјали, технологијата за сечење на плочки се прошири надвор од традиционалните полупроводници базирани на силициум и вклучи нови материјали како галиум нитрид (GaN). Овие нови материјали, поради нивната тврдост и структурни својства, претставуваат нови предизвици за процесите на сечење, што бара понатамошни подобрувања во алатките и техниките за сечење.
Како критичен процес во полупроводничката индустрија, сечењето на плочки продолжува да се оптимизира како одговор на еволуирачките барања и технолошкиот напредок, поставувајќи ја основата за идните технологии за микроелектроника и интегрирани кола.
Подобрувањата во технологијата за сечење на плочки одат подалеку од развојот на помошни материјали и алатки. Тие исто така опфаќаат оптимизација на процесот, подобрувања во перформансите на опремата и прецизна контрола на параметрите на сечење. Овие достигнувања имаат за цел да обезбедат висока прецизност, ефикасност и стабилност во процесот на сечење на плочки, задоволувајќи ја потребата на полупроводничката индустрија за помали димензии, поголема интеграција и посложени структури на чипови.
Област за подобрување | Специфични мерки | Ефекти |
Оптимизација на процеси | - Подобрување на почетните подготовки, како што се попрецизно позиционирање на плочките и планирање на патеката. | - Намалете ги грешките при сечење и подобрете ја стабилноста. |
- Минимизирајте ги грешките при сечење и подобрете ја стабилноста. | - Усвојте механизми за следење во реално време и повратни информации за прилагодување на притисокот, брзината и температурата на алатот. | |
- Пониски стапки на кршење на плочките и подобрување на квалитетот на чипот. | ||
Подобрување на перформансите на опремата | - Користете високопрецизни механички системи и напредна технологија за автоматска контрола. | - Зголемете ја точноста на сечењето и намалете го отпадот од материјал. |
- Воведување на технологија за ласерско сечење соодветна за плотни од материјали со висока тврдост. | - Подобрување на ефикасноста на производството и намалување на рачните грешки. | |
- Зголемување на автоматизацијата на опремата за автоматско следење и прилагодувања. | ||
Прецизна контрола на параметрите | - Фино прилагодете ги параметрите како што се длабочината на сечење, брзината, типот на алатка и методите на ладење. | - Обезбедете интегритет на чипот и електрични перформанси. |
- Прилагодете ги параметрите врз основа на материјалот, дебелината и структурата на плочката. | - Зголемете ги стапките на принос, намалете го отпадот од материјал и намалете ги трошоците за производство. | |
Стратешко значење | - Континуирано истражување на нови технолошки патишта, оптимизирање на процесите и подобрување на капацитетите на опремата за да се задоволат барањата на пазарот. | - Подобрување на приносот и перформансите на производството на чипови, поддршка на развојот на нови материјали и напредни дизајни на чипови. |
1.2 Важноста на сечењето на вафли
Сечењето на вафли игра клучна улога во процесот на производство на полупроводници, директно влијаејќи на последователните чекори, како и на квалитетот и перформансите на финалниот производ. Неговата важност може да се објасни на следниов начин:
Прво, точноста и конзистентноста на сечењето се клучни за обезбедување на принос и сигурност на чипот. За време на производството, плочките минуваат низ повеќе чекори на обработка за да формираат бројни сложени структури на кола, кои мора прецизно да се поделат на поединечни чипови (калапи). Доколку има значителни грешки во усогласувањето или сечењето за време на процесот на сечење, колата може да се оштетат, што влијае на функционалноста и сигурноста на чипот. Затоа, технологијата за сечење со висока прецизност не само што го обезбедува интегритетот на секој чип, туку и спречува оштетување на внатрешните кола, подобрувајќи ја вкупната стапка на принос.
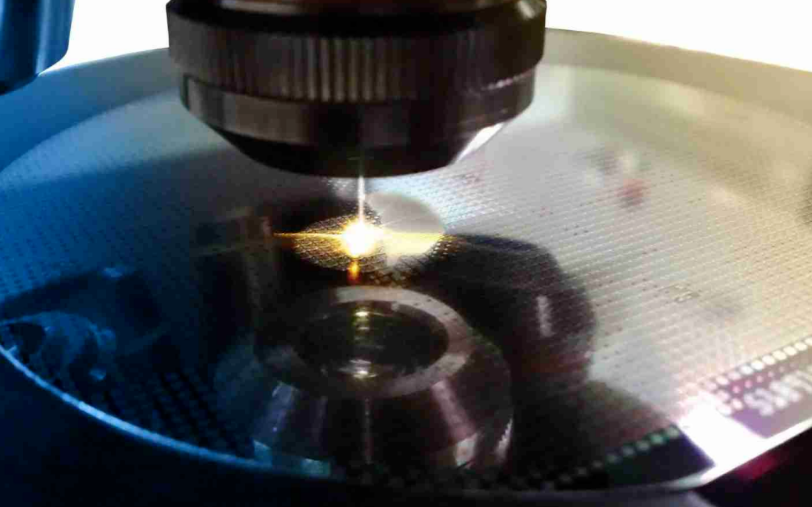
Второ, сечењето на вафли има значително влијание врз ефикасноста на производството и контролата на трошоците. Како клучен чекор во процесот на производство, неговата ефикасност директно влијае на напредокот на последователните чекори. Со оптимизирање на процесот на сечење, зголемување на нивоата на автоматизација и подобрување на брзината на сечење, целокупната ефикасност на производството може значително да се подобри.
Од друга страна, отпадот од материјал за време на сечењето е клучен фактор во управувањето со трошоците. Користењето на напредни технологии за сечење не само што ги намалува непотребните загуби на материјал за време на процесот на сечење, туку и ја зголемува употребата на плочки, со што се намалуваат трошоците за производство.
Со напредокот во полупроводничката технологија, дијаметрите на плочките продолжуваат да се зголемуваат, а густината на колата соодветно се зголемува, што поставува поголеми барања за технологијата за сечење. Поголемите плочки бараат попрецизна контрола на патеките за сечење, особено во областите со кола со висока густина, каде што дури и мали отстапувања можат да предизвикаат дефект на повеќе чипови. Дополнително, поголемите плочки вклучуваат повеќе линии за сечење и посложени чекори во процесот, што наметнува понатамошни подобрувања во прецизноста, конзистентноста и ефикасноста на технологиите за сечење за да се справат со овие предизвици.
1.3 Процес на сечење на вафли
Процесот на сечење на вафли ги опфаќа сите чекори од фазата на подготовка до конечната проверка на квалитетот, при што секоја фаза е клучна за обезбедување на квалитетот и перформансите на сецканите чипови. Подолу е дадено детално објаснување за секоја фаза.
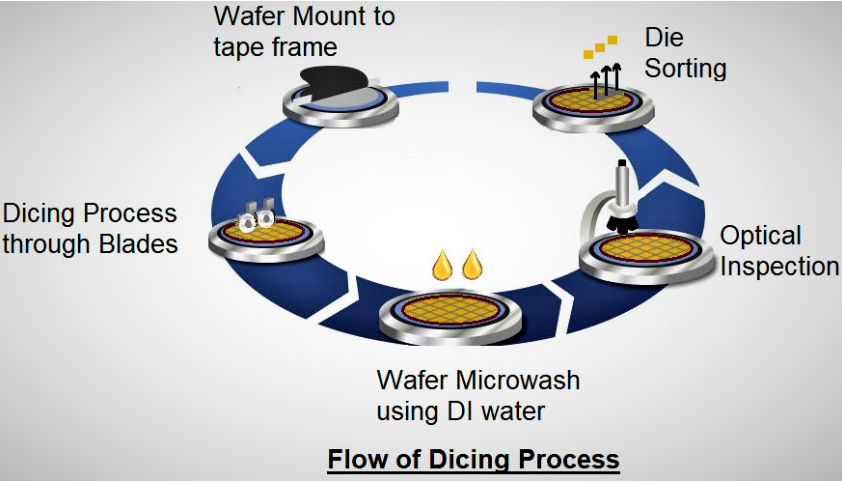
Фаза | Детален опис |
Подготвителна фаза | -Чистење на вафлиКористете вода со висока чистота и специјализирани средства за чистење, во комбинација со ултразвучно или механичко триење, за отстранување на нечистотии, честички и загадувачи, со што ќе се обезбеди чиста површина. -Прецизно позиционирањеКористете опрема со висока прецизност за да се осигурате дека плочката е прецизно поделена по дизајнираните патеки за сечење. -Фиксација на вафлиПрицврстете ја плочката на рамка од лента за да ја одржите стабилноста за време на сечењето, спречувајќи оштетување од вибрации или движење. |
Фаза на сечење | -Сечење на сечилаКористете брзо ротирачки сечила со дијамантска обвивка за физичко сечење, погодни за материјали на база на силикон и исплатливи. -Ласерско сечење коцкиКористете високоенергетски ласерски зраци за бесконтактно сечење, идеално за кршливи или материјали со висока тврдост како галиум нитрид, нудејќи поголема прецизност и помала загуба на материјал. -Нови технологииВоведување на технологии за ласерско и плазма сечење за понатамошно подобрување на ефикасноста и прецизноста, а воедно и минимизирање на зоните погодени од топлина. |
Фаза на чистење | - Користете дејонизирана вода (DI вода) и специјализирани средства за чистење, во комбинација со ултразвучно или спрејско чистење, за отстранување на остатоци и прашина генерирани за време на сечењето, спречувајќи остатоците да влијаат на последователните процеси или електричните перформанси на чипот. - Високочистотата диоксидна вода избегнува воведување на нови загадувачи, обезбедувајќи чиста средина за плочката. |
Фаза на инспекција | -Оптичка инспекцијаКористете оптички системи за детекција во комбинација со алгоритми со вештачка интелигенција за брзо идентификување на дефекти, осигурувајќи дека нема пукнатини или оштетувања на исечените чипови, подобрувајќи ја ефикасноста на инспекцијата и намалувајќи ја човечката грешка. -Мерење на димензиитеПотврдете дека димензиите на чипот ги исполнуваат спецификациите на дизајнот. -Тестирање на електрични перформансиОбезбедете електрични перформанси на критичните чипови да ги исполнуваат стандардите, гарантирајќи сигурност во последователните апликации. |
Фаза на сортирање | - Користете роботски раце или вакуумски чаши за вшмукување за да ги одделите квалификуваните чипови од рамката на лентата и автоматски да ги сортирате врз основа на перформансите, обезбедувајќи ефикасност и флексибилност во производството, а воедно подобрувајќи ја прецизноста. |
Процесот на сечење на плочки вклучува чистење, позиционирање, сечење, чистење, инспекција и сортирање на плочки, при што секој чекор е критичен. Со напредокот во автоматизацијата, ласерското сечење и технологиите за инспекција со вештачка интелигенција, современите системи за сечење на плочки можат да постигнат поголема прецизност, брзина и помала загуба на материјал. Во иднина, новите технологии за сечење, како што се ласер и плазма, постепено ќе го заменат традиционалното сечење на сечила за да ги задоволат потребите на сè посложените дизајни на чипови, дополнително поттикнувајќи го развојот на процесите на производство на полупроводници.
Технологија за сечење на плочки и нејзините принципи
Сликата илустрира три вообичаени технологии за сечење плочки:Сечење на сечила,Ласерско сечење коцки, иПлазма сечењеПодолу е дадена детална анализа и дополнително објаснување на овие три техники:
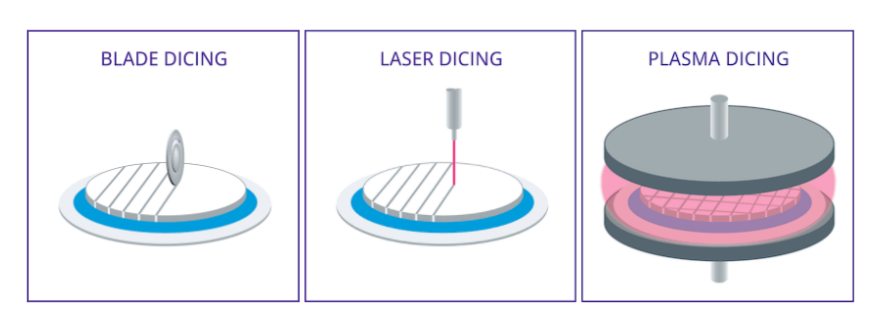
Во производството на полупроводници, сечењето на плочки е клучен чекор што бара избор на соодветен метод на сечење врз основа на дебелината на плочките. Првиот чекор е да се одреди дебелината на плочките. Ако дебелината на плочките надминува 100 микрони, како метод на сечење може да се избере сечење со сечило. Ако сечењето со сечило не е соодветно, може да се користи методот на сечење со фрактури, кој вклучува техники на сечење со стружење и сечење со сечило.
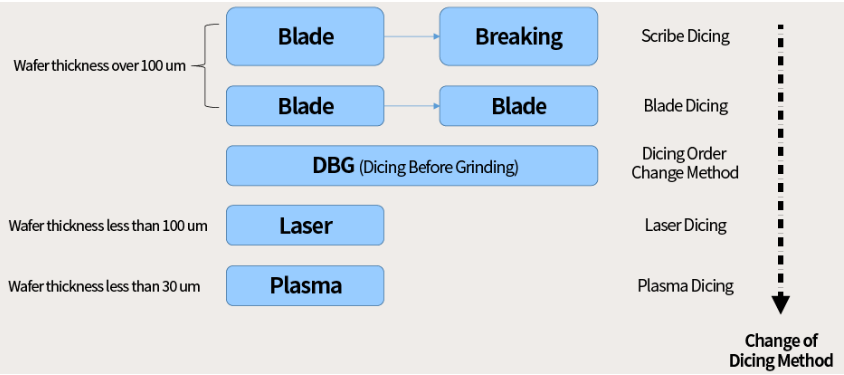
Кога дебелината на плочката е помеѓу 30 и 100 микрони, се препорачува методот DBG (сечење пред мелење). Во овој случај, за да се постигнат најдобри резултати, може да се избере сечење со стругач, сечење со сечило или прилагодување на секвенцата на сечење по потреба.
За ултратенки плочки со дебелина помала од 30 микрони, ласерското сечење станува претпочитан метод поради неговата способност прецизно да сече тенки плочки без да предизвика прекумерно оштетување. Доколку ласерското сечење не може да ги задоволи специфичните барања, како алтернатива може да се користи сечење со плазма. Овој дијаграм на тек обезбедува јасен пат за донесување одлуки за да се обезбеди избор на најсоодветната технологија за сечење плочки под различни услови на дебелина.
2.1 Технологија на механичко сечење
Технологијата на механичко сечење е традиционалниот метод при сечење на плочки. Основниот принцип е да се користи брзо ротирачко дијамантско брусило како алатка за сечење за сечење на плочките. Клучната опрема вклучува вретено со воздушно лежиште, кое го движи алатот за дијамантско брусило со голема брзина за да изврши прецизно сечење или жлебување по претходно дефинирана патека на сечење. Оваа технологија е широко користена во индустријата поради нејзината ниска цена, висока ефикасност и широка применливост.
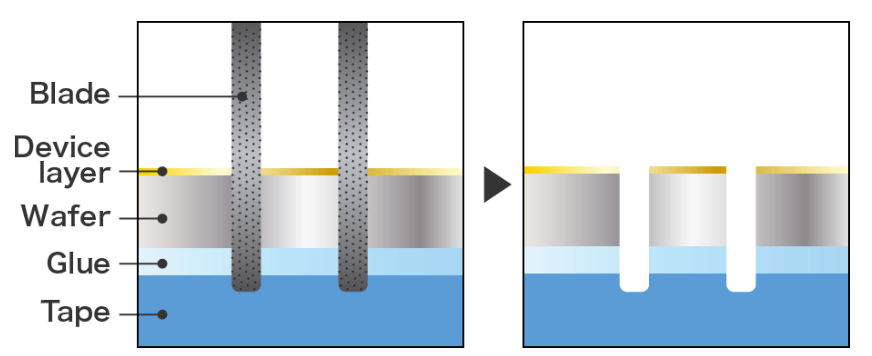
Предности
Високата тврдост и отпорност на абење на алатките за дијамантско брусење овозможуваат технологијата за механичко сечење да се прилагоди на потребите за сечење на различни материјали за плочки, без разлика дали се работи за традиционални материјали на база на силициум или понови сложени полупроводници. Неговото работење е едноставно, со релативно ниски технички барања, што дополнително ја промовира неговата популарност во масовното производство. Дополнително, во споредба со другите методи на сечење како што е ласерското сечење, механичкото сечење има поконтролирани трошоци, што го прави погодно за потребите за производство со голем обем.
Ограничувања
И покрај бројните предности, технологијата на механичко сечење има и ограничувања. Прво, поради физичкиот контакт помеѓу алатот и плочката, прецизноста на сечењето е релативно ограничена, што често доведува до димензионални отстапувања што можат да влијаат на точноста на последователното пакување и тестирање на струготините. Второ, дефекти како што се струготини и пукнатини лесно можат да се појават за време на процесот на механичко сечење, што не само што влијае на стапката на принос, туку може негативно да влијае и на сигурноста и животниот век на струготините. Оштетувањето предизвикано од механички стрес е особено штетно за производството на струготини со висока густина, особено при сечење кршливи материјали, каде што овие проблеми се поизразени.
Технолошки подобрувања
За да се надминат овие ограничувања, истражувачите континуирано го оптимизираат процесот на механичко сечење. Клучните подобрувања вклучуваат подобрување на дизајнот и изборот на материјал на брусилките за подобрување на прецизноста и издржливоста на сечењето. Дополнително, оптимизацијата на структурниот дизајн и системите за контрола на опремата за сечење дополнително ја подобрија стабилноста и автоматизацијата на процесот на сечење. Овие достигнувања ги намалуваат грешките предизвикани од човечки операции и ја подобруваат конзистентноста на сечењата. Воведувањето на напредни технологии за инспекција и контрола на квалитетот за следење на аномалиите во реално време за време на процесот на сечење, исто така, значително ја подобри сигурноста и приносот на сечењето.
Иден развој и нови технологии
Иако технологијата за механичко сечење сè уште има значајно место во сечењето на плочки, новите технологии за сечење брзо напредуваат како што се развиваат полупроводничките процеси. На пример, примената на технологијата за термичко ласерско сечење обезбедува нови решенија за проблемите со прецизноста и дефектите при механичкото сечење. Овој метод на бесконтактно сечење го намалува физичкиот стрес врз плочките, значително намалувајќи ја инциденцата на кршење и пукање, особено при сечење на покршливи материјали. Во иднина, интеграцијата на технологијата за механичко сечење со новите техники на сечење ќе обезбеди производство на полупроводници со повеќе опции и флексибилност, дополнително подобрувајќи ја ефикасноста на производството и квалитетот на чиповите.
Како заклучок, иако технологијата за механичко сечење има одредени недостатоци, континуираните технолошки подобрувања и нејзината интеграција со нови техники на сечење ѝ овозможуваат сè уште да игра важна улога во производството на полупроводници и да ја одржи својата конкурентност во идните процеси.
2.2 Технологија на ласерско сечење
Технологијата за ласерско сечење, како нов метод во сечењето плочки, постепено добива широко внимание во полупроводничката индустрија поради нејзината висока прецизност, недостатокот на механичко оштетување од контакт и можностите за брзо сечење. Оваа технологија ја користи високата густина на енергија и способноста за фокусирање на ласерскиот зрак за да создаде мала зона погодена од топлина на површината на материјалот од плочките. Кога ласерскиот зрак се нанесува на плочките, генерираниот термички стрес предизвикува материјалот да се скрши на означената локација, постигнувајќи прецизно сечење.
Предности на технологијата за ласерско сечење
• Висока прецизностПрецизната способност за позиционирање на ласерскиот зрак овозможува прецизно сечење на ниво на микрон или дури и нанометар, задоволувајќи ги барањата на модерното производство на интегрирани кола со висока прецизност и висока густина.
• Без механички контактЛасерското сечење избегнува физички контакт со плочката, спречувајќи ги вообичаените проблеми при механичкото сечење, како што се кршење и пукање, значително подобрувајќи ја стапката на принос и сигурноста на струготините.
• Голема брзина на сечењеГолемата брзина на ласерското сечење придонесува за зголемена ефикасност на производството, што го прави особено погоден за сценарија за производство во голем обем и со голема брзина.
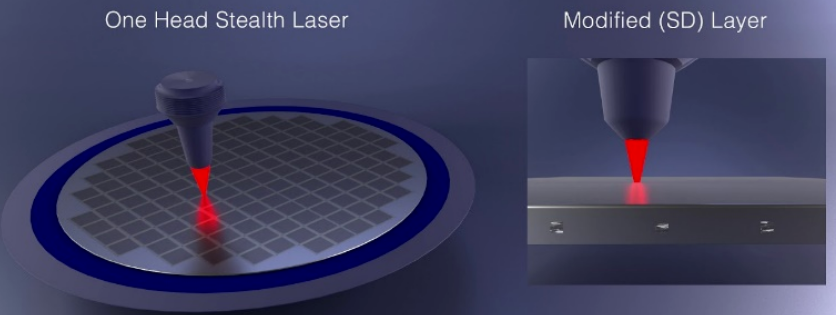
Предизвици со кои се соочуваме
• Висока цена на опрематаПрвичната инвестиција за опрема за ласерско сечење е висока, што претставува економски притисок, особено за малите и средни производствени претпријатија.
• Контрола на сложени процесиЛасерското сечење бара прецизна контрола на неколку параметри, вклучувајќи густина на енергија, позиција на фокус и брзина на сечење, што го прави процесот сложен.
• Проблеми со зоната погодена од топлинаИако бесконтактната природа на ласерското сечење ги намалува механичките оштетувања, термичкиот стрес предизвикан од зоната погодена од топлина (HAZ) може негативно да влијае на својствата на материјалот на плочката. Потребна е понатамошна оптимизација на процесот за да се минимизира овој ефект.
Насоки за технолошко подобрување
За да се справат со овие предизвици, истражувачите се фокусираат на намалување на трошоците за опрема, подобрување на ефикасноста на сечење и оптимизирање на процесот.
• Ефикасни ласери и оптички системиСо развој на поефикасни ласери и напредни оптички системи, можно е да се намалат трошоците за опрема, а воедно да се подобри прецизноста и брзината на сечење.
• Оптимизирање на параметрите на процесотСе спроведуваат длабински истражувања за интеракцијата помеѓу ласерите и материјалите од плочката за да се подобрат процесите што ја намалуваат зоната погодена од топлина, со што се подобрува квалитетот на сечењето.
• Интелигентни контролни системиРазвојот на интелигентни технологии за контрола има за цел да го автоматизира и оптимизира процесот на ласерско сечење, подобрувајќи ја неговата стабилност и конзистентност.
Технологијата за ласерско сечење е особено ефикасна во ултратенки плочки и сценарија за сечење со висока прецизност. Со зголемувањето на големината на плочките и зголемувањето на густината на колата, традиционалните методи на механичко сечење се борат да ги задоволат барањата за висока прецизност и висока ефикасност на модерното производство на полупроводници. Поради своите уникатни предности, ласерското сечење станува претпочитано решение во овие области.
Иако технологијата за ласерско сечење сè уште се соочува со предизвици како што се високите трошоци за опрема и сложеноста на процесот, нејзините уникатни предности во високата прецизност и бесконтактното оштетување ја прават важна насока за развој во производството на полупроводници. Со оглед на тоа што ласерската технологија и интелигентните системи за контрола продолжуваат да напредуваат, се очекува ласерското сечење дополнително да ја подобри ефикасноста и квалитетот на сечењето на плочки, поттикнувајќи го континуираниот развој на полупроводничката индустрија.
2.3 Технологија за сечење со плазма
Технологијата за сечење со плазма, како нов метод за сечење на плочки, привлече значително внимание во последниве години. Оваа технологија користи плазма зраци со висока енергија за прецизно сечење на плочки со контролирање на енергијата, брзината и патеката на сечење на плазма зракот, постигнувајќи оптимални резултати од сечење.
Принцип на работа и предности
Процесот на сечење со плазма се потпира на плазма зрак со висока температура и енергија генериран од опремата. Овој зрак може да го загрее материјалот од плочки до точка на топење или испарување за многу кратко време, овозможувајќи брзо сечење. Во споредба со традиционалното механичко или ласерско сечење, сечењето со плазма е побрзо и создава помала зона погодена од топлина, ефикасно намалувајќи ја појавата на пукнатини и оштетувања за време на сечењето.
Во практични апликации, технологијата за сечење со плазма е особено вешта во ракувањето со плочки со сложени форми. Неговиот високоенергетски, прилагодлив плазма зрак може лесно да сече плочки со неправилна форма со голема прецизност. Затоа, во производството на микроелектроника, особено во производството по нарачка и во мали серии на висококвалитетни чипови, оваа технологија покажува големо ветување за широка употреба.
Предизвици и ограничувања
И покрај многуте предности на технологијата за сечење со плазма, таа се соочува и со некои предизвици.
• Комплексен процесПроцесот на сечење со плазма е сложен и бара опрема со висока прецизност и искусни оператори за да се обезбедиточност и стабилност при сечење.
• Контрола и безбедност на животната срединаВисоката температура и енергијата на плазма зракот бараат строга контрола на животната средина и безбедносни мерки, што ја зголемува сложеноста и трошоците за имплементација.
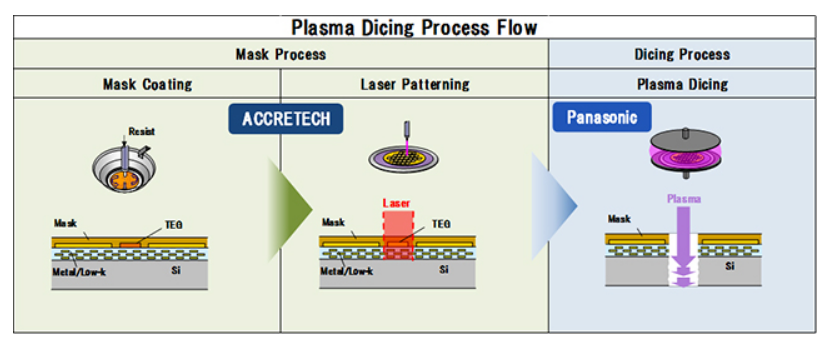
Насоки за иден развој
Со технолошкиот напредок, се очекува предизвиците поврзани со сечењето со плазма постепено да се надминуваат. Со развој на попаметна и постабилна опрема за сечење, зависноста од рачни операции може да се намали, со што се подобрува ефикасноста на производството. Во исто време, оптимизирањето на параметрите на процесот и средината за сечење ќе помогне во намалувањето на безбедносните ризици и оперативните трошоци.
Во полупроводничката индустрија, иновациите во технологијата за сечење и сечење на плочки се клучни за поттикнување на развојот на индустријата. Технологијата за сечење со плазма, со својата висока прецизност, ефикасност и способност за ракување со сложени форми на плочки, се појави како значаен нов играч во оваа област. Иако остануваат некои предизвици, овие прашања постепено ќе се решаваат со континуирани технолошки иновации, носејќи повеќе можности и можности за производство на полупроводници.
Перспективите за примена на технологијата за сечење со плазма се огромни и се очекува таа да игра поважна улога во производството на полупроводници во иднина. Преку континуирани технолошки иновации и оптимизација, сечењето со плазма не само што ќе ги реши постојните предизвици, туку ќе стане и моќен двигател на растот на полупроводничката индустрија.
2.4 Квалитет на сечење и фактори на влијание
Квалитетот на сечењето на плочките е клучен за последователното пакување на чиповите, тестирањето и целокупните перформанси и сигурност на финалниот производ. Вообичаени проблеми што се јавуваат за време на сечењето вклучуваат пукнатини, кршење и отстапувања од сечењето. Овие проблеми се под влијание на неколку фактори што работат заедно.
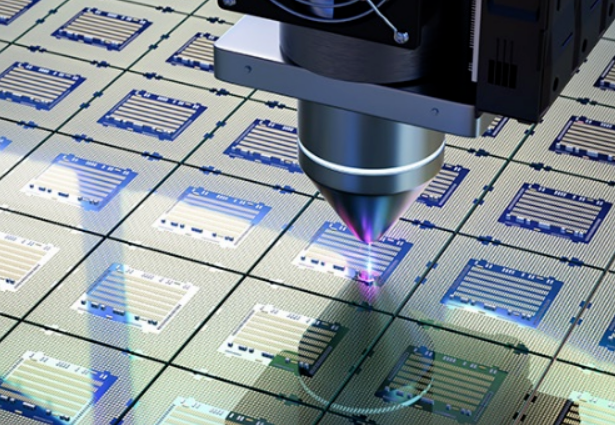
Категорија | Содржина | Влијание |
Параметри на процесот | Брзината на сечење, брзината на напојување и длабочината на сечење директно влијаат врз стабилноста и прецизноста на процесот на сечење. Неправилните поставки можат да доведат до концентрација на стрес и прекумерна зона погодена од топлина, што резултира со пукнатини и кршење. Соодветното прилагодување на параметрите врз основа на материјалот на плочката, дебелината и барањата за сечење е клучно за постигнување на посакуваните резултати од сечењето. | Точните параметри на процесот обезбедуваат прецизно сечење и го намалуваат ризикот од дефекти како што се пукнатини и кршење. |
Опрема и материјални фактори | -Квалитет на сечилотоМатеријалот, тврдоста и отпорноста на абење на сечилото влијаат врз мазноста на процесот на сечење и рамноста на површината за сечење. Сечилата со слаб квалитет го зголемуваат триењето и термичкиот стрес, што потенцијално може да доведе до пукнатини или кршење. Изборот на вистинскиот материјал за сечилото е клучен. -Перформанси на течноста за ладењеТечностите за ладење помагаат во намалувањето на температурата на сечење, минимизирање на триењето и чистење на остатоците. Неефикасното средство за ладење може да доведе до високи температури и натрупување на остатоци, што влијае на квалитетот и ефикасноста на сечењето. Изборот на ефикасни и еколошки средства за ладење е од витално значење. | Квалитетот на сечилото влијае на прецизноста и мазноста на сечењето. Неефикасното средство за ладење може да резултира со лош квалитет и ефикасност на сечење, нагласувајќи ја потребата од оптимална употреба на средството за ладење. |
Контрола на процеси и инспекција на квалитет | -Контрола на процесотСледење во реално време и прилагодување на клучните параметри на сечење за да се обезбеди стабилност и конзистентност во процесот на сечење. -Инспекција на квалитетПроверките на изгледот по сечењето, димензионалните мерења и тестирањето на електричните перформанси помагаат брзо да се идентификуваат и решат проблемите со квалитетот, подобрувајќи ја точноста и конзистентноста на сечењето. | Соодветната контрола на процесот и проверката на квалитетот помагаат да се обезбедат конзистентни, висококвалитетни резултати од сечењето и рано откривање на потенцијални проблеми. |

Подобрување на квалитетот на сечење
Подобрувањето на квалитетот на сечењето бара сеопфатен пристап што ги зема предвид параметрите на процесот, изборот на опрема и материјал, контролата на процесот и инспекцијата. Со континуирано усовршување на технологиите за сечење и оптимизирање на методите на процесот, прецизноста и стабилноста на сечењето на плочки може дополнително да се подобрат, обезбедувајќи посигурна техничка поддршка за индустријата за производство на полупроводници.
#03 Ракување и тестирање по сечењето
3.1 Чистење и сушење
Чекорите за чистење и сушење по сечењето на плочките се клучни за обезбедување на квалитет на струготини и непречен тек на последователните процеси. Во текот на оваа фаза, важно е темелно да се отстранат остатоците од силикон, остатоците од течноста за ладење и другите загадувачи генерирани за време на сечењето. Подеднакво е важно да се осигура дека струготините не се оштетени за време на процесот на чистење, а по сушењето, да се осигура дека нема влага на површината на струготините за да се спречат проблеми како што се корозија или електростатско празнење.
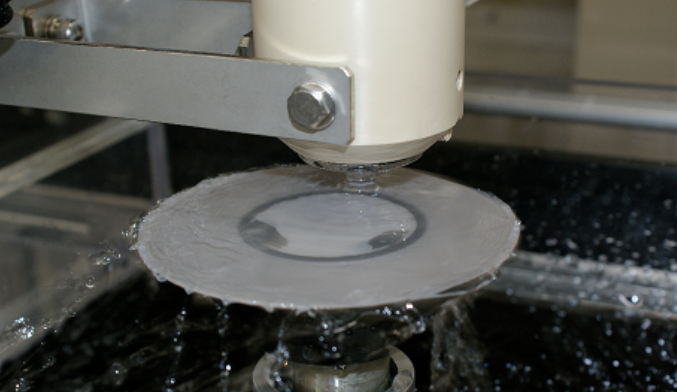
Ракување по сечењето: Процес на чистење и сушење
Чекор на процесот | Содржина | Влијание |
Процес на чистење | -МетодКористете специјализирани средства за чистење и чиста вода, во комбинација со ултразвучни или механички техники на четкање за чистење. | Обезбедува темелно отстранување на нечистотиите и спречува оштетување на струготините за време на чистењето. |
-Избор на средство за чистењеИзберете врз основа на материјалот на плочката и видот на загадувач за да се обезбеди ефикасно чистење без оштетување на чипот. | Правилниот избор на средство е клучен за ефикасно чистење и заштита од стружења. | |
-Контрола на параметриСтрого контролирајте ја температурата, времето и концентрацијата на растворот за чистење за да спречите проблеми со квалитетот предизвикани од неправилно чистење. | Контролите помагаат да се избегне оштетување на плочката или оставање загадувачи, со што се обезбедува конзистентен квалитет. | |
Процес на сушење | -Традиционални методиСушење со природен воздух и сушење со топол воздух, кои имаат ниска ефикасност и можат да доведат до насобирање на статички електрицитет. | Може да резултира со побавно време на сушење и потенцијални проблеми со статичкиот електростат. |
-Модерни технологииКористете напредни технологии како што се вакуумско сушење и инфрацрвено сушење за да се осигурате дека чипсот брзо се суши и да се избегнат штетни ефекти. | Побрз и поефикасен процес на сушење, со што се намалува ризикот од статичко празнење или проблеми поврзани со влага. | |
Избор и одржување на опрема | -Избор на опремаМашините за чистење и сушење со висок квалитет ја подобруваат ефикасноста на обработката и прецизно ги контролираат потенцијалните проблеми за време на ракувањето. | Висококвалитетните машини обезбедуваат подобра обработка и ја намалуваат веројатноста за грешки при чистење и сушење. |
-Одржување на опремаРедовната инспекција и одржување на опремата гарантираат дека таа останува во оптимална работна состојба, гарантирајќи го квалитетот на чипот. | Правилното одржување спречува дефекти на опремата, обезбедувајќи сигурна и висококвалитетна обработка. |
Чистење и сушење по сечењето
Чекорите на чистење и сушење по сечењето на плочките се сложени и деликатни процеси кои бараат внимателно разгледување на повеќе фактори за да се обезбеди конечниот резултат од обработката. Со користење на научни методи и ригорозни процедури, можно е да се осигура дека секој чип влегува во последователните фази на пакување и тестирање во оптимална состојба.
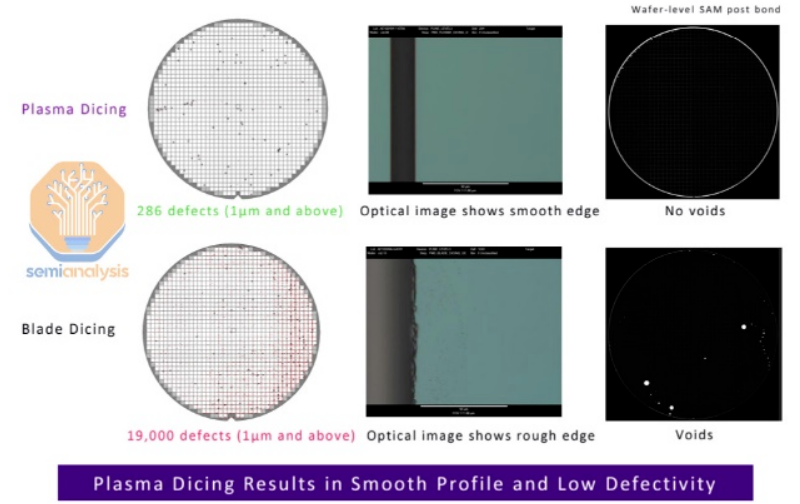
Инспекција и тестирање по сечењето
Чекор | Содржина | Влијание |
Чекор за инспекција | 1.Визуелна инспекцијаКористете опрема за визуелна или автоматска инспекција за да проверите за видливи дефекти како што се пукнатини, кршење или контаминација на површината на струготините. Брзо идентификувајте ги физички оштетените струготини за да избегнете отпад. | Помага во идентификување и отстранување на неисправни струготини во раната фаза од процесот, намалувајќи ја загубата на материјал. |
2.Мерење на големинатаКористете прецизни мерни уреди за прецизно мерење на димензиите на струготините, осигурувајќи се дека големината на исечокот ги исполнува спецификациите на дизајнот и спречувајќи проблеми со перформансите или тешкотии со пакувањето. | Обезбедува чиповите да бидат во рамките на потребните граници на големината, спречувајќи деградација на перформансите или проблеми со склопувањето. | |
3.Тестирање на електрични перформансиОценете ги клучните електрични параметри како што се отпор, капацитивност и индуктивност, за да ги идентификувате несоодветните чипови и да се осигурате дека само чипови со квалификации за перформанси продолжуваат во следната фаза. | Обезбедува само функционални и тестирани перформанси чипови да се движат напред во процесот, намалувајќи го ризикот од дефект во подоцнежните фази. | |
Чекор за тестирање | 1.Функционално тестирањеПотврдете дека основната функционалност на чипот работи како што е предвидено, идентификувајќи ги и елиминирајќи ги чиповите со функционални абнормалности. | Обезбедува чиповите да ги исполнуваат основните оперативни барања пред да преминат во подоцнежни фази. |
2.Тестирање на сигурностОценете ја стабилноста на перформансите на чипот при продолжена употреба или сурови средини, што обично вклучува стареење на висока температура, тестирање на ниска температура и тестирање на влажност за симулирање на екстремни услови во реалниот свет. | Обезбедува сигурно функционирање на чиповите под различни услови на животната средина, подобрувајќи го долготрајноста и стабилноста на производот. | |
3.Тестирање на компатибилностПроверете дали чипот работи правилно со други компоненти или системи, осигурувајќи се дека нема грешки или влошување на перформансите поради некомпатибилност. | Обезбедува непречено работење во апликации од реалниот свет со спречување на проблеми со компатибилноста. |
3.3 Пакување и складирање
По сечењето на плочките, чиповите се клучен резултат од процесот на производство на полупроводници, а фазите на нивното пакување и складирање се подеднакво важни. Соодветните мерки за пакување и складирање се неопходни не само за да се обезбеди безбедноста и стабилноста на чиповите за време на транспортот и складирањето, туку и за да се обезбеди силна поддршка за последователните фази на производство, тестирање и пакување.
Резиме на фазите на инспекција и тестирање:
Чекорите за инспекција и тестирање на чипови по сечење на плочки опфаќаат низа аспекти, вклучувајќи визуелна инспекција, мерење на големината, тестирање на електричните перформанси, функционално тестирање, тестирање на сигурноста и тестирање на компатибилност. Овие чекори се меѓусебно поврзани и комплементарни, формирајќи цврста бариера за да се обезбеди квалитет и сигурност на производот. Преку строги процедури за инспекција и тестирање, потенцијалните проблеми можат да се идентификуваат и решат брзо, осигурувајќи дека финалниот производ ги исполнува барањата и очекувањата на клиентите.
Аспект | Содржина |
Мерки за пакување | 1.АнтистатикМатеријалите за пакување треба да имаат одлични антистатички својства за да се спречи статичкиот електрицитет да ги оштети уредите или да влијае на нивните перформанси. |
2.Отпорен на влагаМатеријалите за пакување треба да имаат добра отпорност на влага за да се спречи корозија и влошување на електричните перформанси предизвикани од влажност. | |
3.Отпорен на удариМатеријалите за пакување треба да обезбедат ефикасна апсорпција на удари за да ги заштитат чиповите од вибрации и удари за време на транспортот. | |
Околина за складирање | 1.Контрола на влажностСтрого контролирајте ја влажноста во соодветен опсег за да спречите апсорпција на влага и корозија предизвикани од прекумерна влажност или статички проблеми предизвикани од ниска влажност. |
2.ЧистотаОдржувајте чиста средина за складирање за да избегнете контаминација на чиповите со прашина и нечистотии. | |
3.Контрола на температуратаПоставете разумен температурен опсег и одржувајте ја стабилноста на температурата за да спречите забрзано стареење поради прекумерна топлина или проблеми со кондензација предизвикани од ниски температури. | |
Редовна инспекција | Редовно проверувајте и оценувајте ги складираните чипови, користејќи визуелни инспекции, мерења на големината и тестови за електрични перформанси за навремено идентификување и решавање на потенцијални проблеми. Врз основа на времето и условите за складирање, планирајте ја употребата на чиповите за да се осигурате дека се користат во оптимална состојба. |
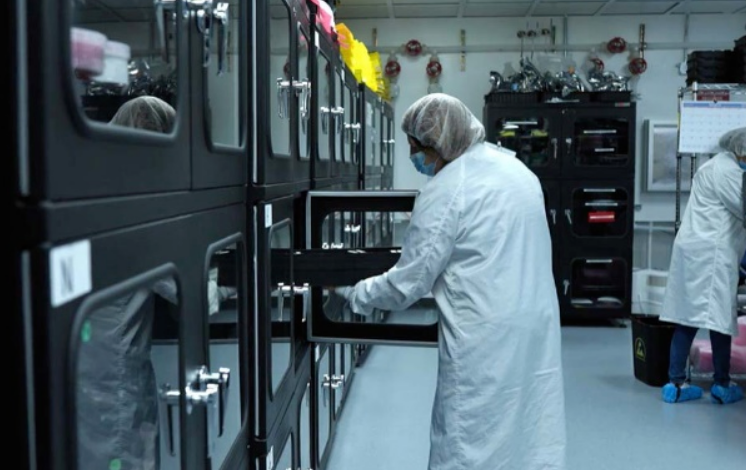
Проблемот со микропукнатини и оштетувања за време на процесот на сечење на плочките е значаен предизвик во производството на полупроводници. Стресот при сечење е главната причина за овој феномен, бидејќи создава мали пукнатини и оштетувања на површината на плочките, што доведува до зголемени трошоци за производство и намалување на квалитетот на производот.
За да се справиме со овој предизвик, клучно е да се минимизира стресот при сечење и да се имплементираат оптимизирани техники, алатки и услови за сечење. Внимателното внимание на фактори како што се материјалот на сечилото, брзината на сечење, притисокот и методите на ладење може да помогне во намалувањето на формирањето на микропукнатини и подобрување на целокупниот принос од процесот. Дополнително, тековните истражувања за понапредни технологии за сечење, како што е ласерското сечење, истражуваат начини за понатамошно ублажување на овие проблеми.
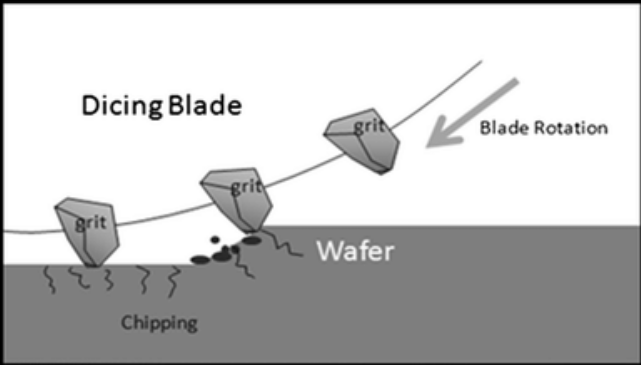
Како кршлив материјал, плочките се склони кон внатрешни структурни промени кога се подложени на механички, термички или хемиски стрес, што доведува до формирање на микропукнатини. Иако овие пукнатини може да не бидат веднаш забележливи, тие можат да се прошират и да предизвикаат посериозни оштетувања како што напредува процесот на производство. Ова прашање станува особено проблематично за време на последователните фази на пакување и тестирање, каде што температурните флуктуации и дополнителните механички стресови можат да предизвикаат овие микропукнатини да се развијат во видливи фрактури, што потенцијално може да доведе до дефект на чипот.
За да се ублажи овој ризик, од суштинско значење е внимателно да се контролира процесот на сечење со оптимизирање на параметри како што се брзината на сечење, притисокот и температурата. Користењето помалку агресивни методи на сечење, како што е ласерското сечење, може да го намали механичкиот стрес врз плочката и да го минимизира формирањето на микропукнатини. Дополнително, имплементацијата на напредни методи за инспекција како што се инфрацрвено скенирање или рендгенско снимање за време на процесот на сечење на плочката може да помогне во откривањето на овие пукнатини во рана фаза пред да предизвикаат понатамошно оштетување.
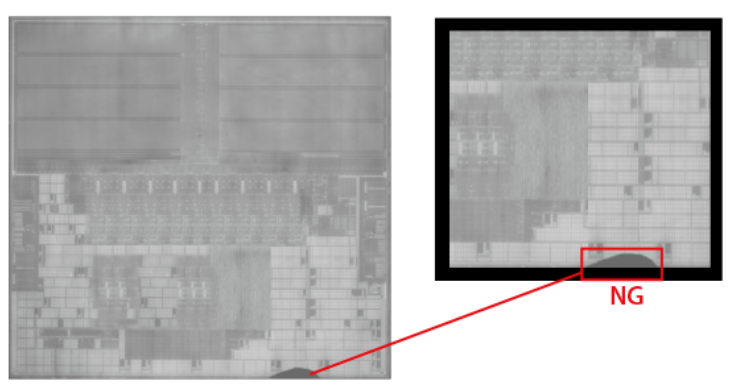
Оштетувањето на површината на плочката е значаен проблем во процесот на сечење, бидејќи може да има директно влијание врз перформансите и сигурноста на чипот. Таквата штета може да биде предизвикана од неправилна употреба на алатки за сечење, неточни параметри на сечење или дефекти на материјалот својствени за самата плочка. Без оглед на причината, овие оштетувања можат да доведат до промени во електричниот отпор или капацитетот на колото, што влијае на целокупните перформанси.
За да се решат овие проблеми, се разгледуваат две клучни стратегии:
1. Оптимизирање на алатките за сечење и параметритеСо користење на поостри сечила, прилагодување на брзината на сечење и модифицирање на длабочината на сечење, концентрацијата на стрес за време на процесот на сечење може да се минимизира, со што се намалува потенцијалот за оштетување.
2. Истражување на нови технологии за сечењеНапредните техники како ласерско сечење и плазма сечење нудат подобрена прецизност, а воедно потенцијално го намалуваат нивото на оштетување на плочката. Овие технологии се изучуваат за да се пронајдат начини за постигнување висока точност на сечење, а воедно и минимизирање на термичкиот и механичкиот стрес на плочката.
Термичка површина на удар и нејзините ефекти врз перформансите
Во процесите на термичко сечење, како што се ласерското и плазма сечењето, високите температури неизбежно создаваат зона на термичко влијание на површината на плочата. Оваа област, каде што градиентот на температурата е значаен, може да ги промени својствата на материјалот, влијаејќи на конечните перформанси на чипот.
Влијание на термички засегнатата зона (TAZ):
Промени во кристалната структураПод високи температури, атомите во материјалот на плочката може да се преуредуваат, предизвикувајќи нарушувања во кристалната структура. Ова нарушување го ослабува материјалот, намалувајќи ја неговата механичка цврстина и стабилност, што го зголемува ризикот од дефект на чипот за време на употребата.
Промени во електричните својстваВисоките температури можат да ја променат концентрацијата и подвижноста на носачите во полупроводничките материјали, влијаејќи на електричната спроводливост на чипот и ефикасноста на пренос на струја. Овие промени може да доведат до пад на перформансите на чипот, што потенцијално го прави несоодветен за наменетата намена.
За да се ублажат овие ефекти, контролата на температурата за време на сечењето, оптимизирањето на параметрите на сечење и истражувањето на методи како што се млазници за ладење или третмани по обработката се основни стратегии за намалување на степенот на термичко влијание и одржување на интегритетот на материјалот.
Генерално, и микропукнатините и зоните на термичко влијание се клучни предизвици во технологијата за сечење на плочки. Континуираното истражување, заедно со технолошкиот напредок и мерките за контрола на квалитетот, ќе биде неопходно за подобрување на квалитетот на полупроводничките производи и зголемување на нивната конкурентност на пазарот.
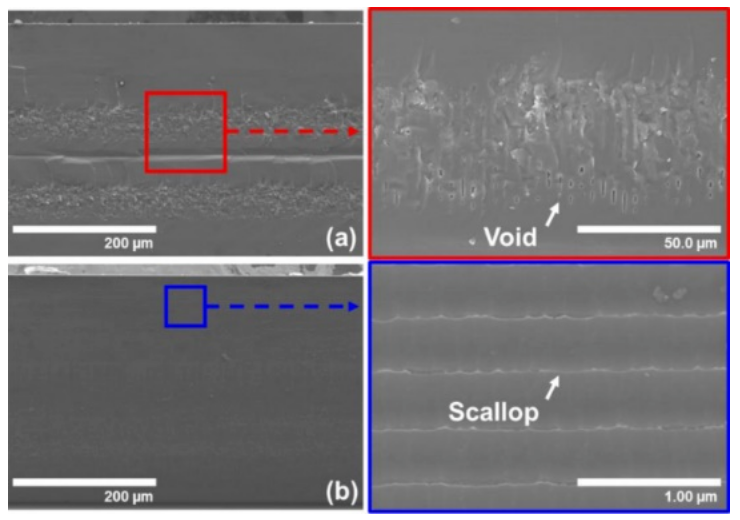
Мерки за контрола на зоната на термичко влијание:
Оптимизирање на параметрите на процесот на сечењеНамалувањето на брзината и моќноста на сечење може ефикасно да ја минимизира големината на зоната на термичко влијание (TAZ). Ова помага во контролирањето на количината на топлина генерирана за време на процесот на сечење, што директно влијае на својствата на материјалот на плочката.
Напредни технологии за ладењеПримената на технологии како ладење со течен азот и микрофлуидно ладење може значително да го ограничи опсегот на зоната на термичко влијание. Овие методи на ладење помагаат поефикасно да се распрсне топлината, со што се зачувуваат својствата на материјалот на плочката и се минимизира термичкото оштетување.
Избор на материјалИстражувачите истражуваат нови материјали, како што се јаглеродни наноцевки и графен, кои поседуваат одлична топлинска спроводливост и механичка цврстина. Овие материјали можат да ја намалат зоната на термичко влијание, а воедно да ги подобрат целокупните перформанси на чиповите.
Накратко, иако зоната на термичко влијание е неизбежна последица од технологиите за термичко сечење, таа може ефикасно да се контролира преку оптимизирани техники на обработка и избор на материјал. Идните истражувања веројатно ќе се фокусираат на фино подесување и автоматизирање на процесите на термичко сечење за да се постигне поефикасно и попрецизно сечење на плочки.

Стратегија за рамнотежа:
Постигнувањето на оптимална рамнотежа помеѓу приносот на вафли и ефикасноста на производството е постојан предизвик во технологијата за сечење вафли. Производителите треба да земат предвид повеќе фактори, како што се побарувачката на пазарот, трошоците за производство и квалитетот на производот, за да развијат рационална стратегија за производство и параметри на процесот. Во исто време, воведувањето напредна опрема за сечење, подобрувањето на вештините на операторите и подобрувањето на контролата на квалитетот на суровините се од суштинско значење за одржување или дури и подобрување на приносот, а воедно и зголемување на ефикасноста на производството.
Идни предизвици и можности:
Со напредокот на полупроводничката технологија, сечењето плочки се соочува со нови предизвици и можности. Како што се намалуваат големините на чиповите, а интеграцијата се зголемува, барањата за прецизност и квалитет на сечење значително растат. Истовремено, новите технологии нудат нови идеи за развој на техники за сечење плочки. Производителите мора да останат во тек со динамиката на пазарот и технолошките трендови, постојано прилагодувајќи ги и оптимизирајќи ги производствените стратегии и параметрите на процесот за да ги задоволат промените на пазарот и технолошките барања.
Како заклучок, со интегрирање на размислувањата за побарувачката на пазарот, трошоците за производство и квалитетот на производот, како и со воведување на напредна опрема и технологија, подобрување на вештините на операторите и зајакнување на контролата на суровините, производителите можат да постигнат најдобра рамнотежа помеѓу приносот на плочки и ефикасноста на производството за време на сечењето на плочките, што доведува до ефикасно и висококвалитетно производство на полупроводнички производи.
Идни перспективи:
Со брзиот технолошки напредок, полупроводничката технологија напредува со невидено темпо. Како клучен чекор во производството на полупроводници, технологијата за сечење плочки е подготвена за возбудливи нови случувања. Гледајќи напред, се очекува технологијата за сечење плочки да постигне значителни подобрувања во прецизноста, ефикасноста и цената, внесувајќи нова виталност во континуираниот раст на полупроводничката индустрија.
Зголемување на прецизноста:
Во потрага по поголема прецизност, технологијата за сечење на плочки постојано ќе ги поместува границите на постојните процеси. Со длабинско проучување на физичките и хемиските механизми на процесот на сечење и прецизно контролирање на параметрите на сечење, ќе се постигнат пофини резултати од сечење за да се задоволат сè посложените барања за дизајн на кола. Дополнително, истражувањето на нови материјали и методи на сечење значително ќе го подобри приносот и квалитетот.
Зголемување на ефикасноста:
Новата опрема за сечење плочки ќе се фокусира на паметен и автоматизиран дизајн. Воведувањето на напредни системи за контрола и алгоритми ќе овозможи опремата автоматски да ги прилагодува параметрите на сечење за да ги задоволи различните барања за материјали и дизајн, со што значително ќе се подобри ефикасноста на производството. Иновациите како што се технологијата за сечење со повеќе плочки и системите за брза замена на сечилата ќе играат клучна улога во подобрувањето на ефикасноста.
Намалување на трошоците:
Намалувањето на трошоците е клучна насока за развој на технологијата за сечење плочки. Со развојот на нови материјали и методи на сечење, се очекува трошоците за опрема и трошоците за одржување ефикасно да се контролираат. Дополнително, оптимизацијата на производствените процеси и намалувањето на стапките на отпад дополнително ќе го намалат отпадот за време на производството, што ќе доведе до намалување на вкупните трошоци за производство.
Паметно производство и IoT:
Интеграцијата на паметното производство и технологиите „Интернет на нештата“ (IoT) ќе донесе трансформативни промени во технологијата за сечење плочки. Преку меѓусебна поврзаност и споделување податоци помеѓу уредите, секој чекор од процесот на производство може да се следи и оптимизира во реално време. Ова не само што ја подобрува ефикасноста на производството и квалитетот на производот, туку им обезбедува на компаниите попрецизно предвидување на пазарот и поддршка при донесување одлуки.
Во иднина, технологијата за сечење плочки ќе постигне извонреден напредок во прецизноста, ефикасноста и цената. Овие достигнувања ќе го поттикнат континуираниот развој на полупроводничката индустрија и ќе донесат повеќе технолошки иновации и погодности за човечкото општество.
Време на објавување: 19 ноември 2024 година